От сырья до сапога: как в Томске делают резиновую обувь
Рассказываем, чем сегодня живет Томский завод резиновой обуви
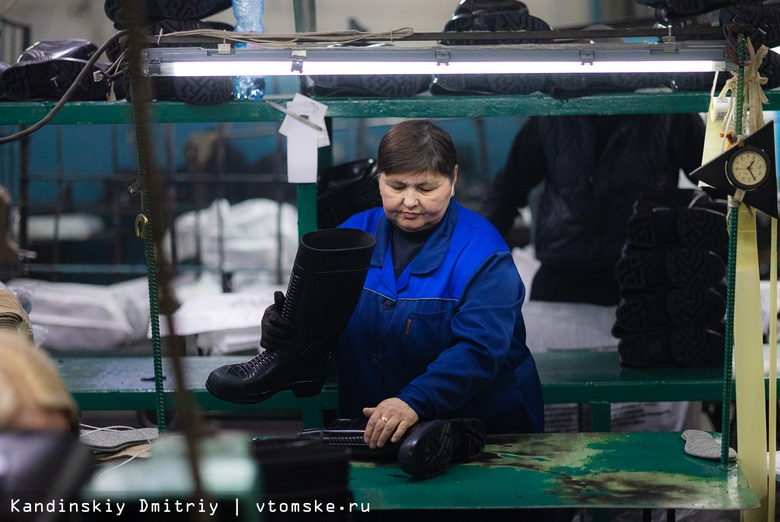
В 2022 году Томскому заводу резиновой обуви (ТЗРО) исполнилось 80 лет. По словам сотрудников компании, многие томичи думают, что завод давно закрылся, хотя это не так. Сегодня предприятие выпускает обувь из резины, полиуретана и других материалов. А недавно ТЗРО запустил в работу новое оборудование для выпуска специализированной обуви.
В рамках рубрики «Знай город» мы уже рассказывали о работе многих местных предприятий: «Томские мельницы», «Сибкабель», ТЭМЗ, «Деревенское молочко», «Эскимос» и другие (можно посмотреть тут).
Теперь мы отправились на завод резиновой обуви, чтобы посмотреть, чем живет сегодня предприятие и как его работники делают сапоги.
***
Немного истории. Томский завод резиновой обуви основан в 1942 году на базе эвакуированного из Москвы предприятия «Красный богатырь». Изначально завод разместился на площади Ленина, где сейчас находится Богоявленский собор. Первые два года предприятие выпускало продукцию для нужд Красной армии: противогазы, резину для танков, амортизаторы для самолетов, резиновые перчатки для защиты от боевых отравляющих веществ.
С конца 1944 года завод перешел на выпуск обуви для обычного населения — это были клееные галоши. Со временем ассортимент расширялся.
В 1960-х прошла реконструкция завода; производство перенесли на промышленную площадку по проспекту Ленина, 217. Здесь предприятие находится до сих пор, но уже на меньших площадях. К концу 1980-х на заводе выпускали до 120 тысяч пар обуви в сутки.
Завод сегодня
В наши дни томское предприятие выпускает в год более двух миллионов пар обуви разных моделей. А еще резиновые шланги, шайбы для хоккея и другие резинотехнические изделия. На предприятии трудятся порядка 430 человек.
— В 2022 году заводу исполнилось 80 лет. Хотя томичи вообще считают, что предприятия больше нет. Мол, раньше был гигантский завод, а сейчас только торговые площади остались. Мы видим подобные комментарии в социальных сетях, — говорит председатель совета директоров ТЗРО Юрий Игнатов. — Но по России и в других странах нас хорошо знают. У нас есть модели, которые в мире практически никто больше не делает.
В 2020 году на предприятии появился современный литьевой агрегат из Италии. Оборудование делали на заказ, поясняет Игнатов. С помощью него делают сапоги из полиуретана по уникальной технологии. А в конце 2022 года на заводе установили второй литьевой агрегат, недавно завершилась его окончательная пусконаладка. Новое оборудование, по словам Игнатова, завод покупал за счет собственных средств.
— В большей степени предприятие сегодня нацелено на выпуск специализированной обуви. Это сапоги, в которых при сложных условиях могут работать, например, шахтеры или пожарные, — поясняет директор ТЗРО Елена Шайдюк. — В меньшем количестве производим обувь для активного отдыха, повседневную обувь для мужчин, женщин и детей.
В целом завод делает обувь из резины, полиуретана, термоэластопласта, ЭВА и ПВХ.
Елена Шайдюк
Чем отличаются материалы?
Резиновые сапоги делаются из натурального каучука. Такая обувь не промокает, она очень эластичная и износостойкая, в ней не будет скользко на льду, она хорошо защищает ноги от агрессивной среды (щелочи, масла, бензин). Минус — резина дубеет на морозе и не защищает от холода.
Полиуретан — это синтетический материал, создающийся путем соединения нескольких полимеров. Процесс объединения образует вспененную структуру, в результате чего материал обладает упругостью, эластичностью и сравнительно небольшим весом. Сапоги из полиуретана хорошо держат тепло, защищают от воды, агрессивных сред, механических повреждений.
ЭВА (EVA) — сокращенное название от этиленвинилацетата. Это вспененный полимер с пористой структурой. Из него делают обувь (сапоги, сланцы, галоши), а еще коврики для машин. У этого материала хорошая теплозащита, устойчивость к влаге, легкий вес. Но обувь из ЭВА плохо выдерживает механические повреждения.
ПВХ (поливинилхлорид) — это один из видов пластмассы, водонепроницаемый, гипоаллергенный материал. Обувь из ПВХ изготавливают методом литья при высокой температуре. Такие сапоги и ботинки носят в быту, на химических производствах, в лабораториях. Но ПВХ-обувь подходит только для плюсовых температур.
Термоэластопластпласт (ТЭП) — наиболее популярный материал для изготовления подошвы в обувной промышленности. Термоэластопласт сочетает в себе преимущества термопластов и каучука, благодаря чему обладает высокими защитными свойствами. С помощью современных технологий производители делают обувь с литьевой подошвой из ТЭП. Такой метод соединения верха и подошвы на сегодняшний день считается самым надежным и герметичным в обувной промышленности.
Вместе с директором завода мы отправляемся на экскурсию по цехам.
Все начинается с идеи
Рождение новой модели обуви происходит в голове, с мысли «А что нового мы можем сделать?» Когда появляются первые идеи, за работу берутся сотрудники модельно-конструкторского отдела завода. Их задача — придать идее графический и материальный вид: это наброски рисунков, печать эскизов новой обуви на 3D-принтере, примерка напечатанного сапога на колодку, подборка всех необходимых составляющих (подносок, стельки, каблук и прочее).
Конструкторы делают несколько разных рисунков, из которых выбирают лучший вариант. Первые наброски делаются от руки, далее — с помощью графического планшета, чтобы точнее отработать детали.
— Каждый раз мы стараемся придумать что-нибудь новое, — говорит художник-конструктор Надежда Бараулина. — Когда эскизы согласованы, мы переходим к чертежам. Для одной модели делаем целый комплект чертежей. После этого уже подключаем к работе 3D-принтер. Он нужен, чтобы сделать твердотельную модель.
Напечатанная на принтере модель позволяет сделать замеры, понять, насколько хорошо все было сконструировано, как визуально будет смотреться обувь, поясняет директор завода Елена Шайдюк.
По 3D-модели ботинка далее будут делать пресс-форму, чтобы отливать сапоги (из полиуретана). После пробной отливки сотрудники снова проверяют все параметры, при необходимости что-то корректируют.
Когда модель новой обуви проходит тест, завод заказывает серию пресс-форм на весь размерный ряд.
Проверка на тянучесть
На томском заводе реализован полный цикл производства обуви из резины: от резиносмешения до выпуска конечного продукта. Каучук компания покупает у других предприятий в России. Но прежде чем отправить большую партию в производство, в работу включается испытательная лаборатория.
Это место как маленький завод. В лаборатории есть свои резиносмеситель, пресс, вальцовочный станок и другое оборудование для тестирования материалов. Недавно лаборатория тоже получила новое оборудование.
Из каждой новой партии каучука сотрудники лаборатории берут пробу и проводят испытания: смотрят, соответствует ли сырье необходимым физико-механическим свойствам. После положительного заключения лаборатории каучук попадает в основной цех.
Эта работа идет каждый день с самого утра, когда завод открывается. Так как мы посещали предприятие ближе к обеденному времени, свою работу на день лаборатория уже завершила. Но лаборант Нина Голикова показала нам на уже проверенной партии, как каучук проверяют на предел прочности при разрыве.
Нина Игоревна работает на заводе не один десяток лет, это легко заметить по тому, как быстро она проводит все замеры. Специалист вырезала небольшой кусочек резины, замерила его толщину, после чего началось испытание.
Проверка происходит с помощью разрывных машин с весами. Оборудование растягивает кусочек резины до тех пор, пока он не порвется. По специальной формуле высчитывается предел прочности.
— На каждую резину есть свои нормы в килограммах и процентах, — добавляет лаборант.
Проверка резины — не единственное, что делают сотрудники. В лаборатории также испытывают клей, гибкость подошвы и так далее. Здесь полноценный входной контроль.
Далее мы отправляемся в цеха, где делают обувь из резины.
Как резина в обувь превращается
Процесс создания резиновой обуви начинается с цеха резиносмешения. Здесь происходит производство резиновой смеси на основе синтетических каучуков общего и специального назначения, а также химических ингредиентов (выполняющих функцию наполнителей, пластификаторов, стабилизаторов, активаторов и вулканизующих агентов).
Смешивание компонентов происходит в закрытой камере резиносмесителя роторного типа. После перемешивания до однородного состояния огромные куски резины попадают на горячие вальцовочные станки. Вальцы превращают резиновое «тесто» в огромные по ширине и длине пластины.
Затем резиновая смесь поступает на механизированную поточную линию, включающую подогревательные вальцы, резинообрабатывающий каландр, охладительные и закройные установки. Из резиновых полотен вырезают заготовки разной формы для дальнейшей сборки.
На томском заводе резиновая обувь по методу изготовления подразделяется на клееную и формовую.
— Далее мы попадаем в цех клееной обуви. Здесь пласты резины еще раз раскатывают до нужной толщины. Она может быть разной, так как есть подошва из резины, есть верха, каблуки, соединительные детали, — поясняет директор завода Елена Шайдюк. — Из тонких пластов резины по выкройкам вырезаются заготовки для будущей обуви. Из толстых кусков на специальном станке выбиваются каблуки и подошва. Неиспользованные остатки снова отправляются на вальцы для повторного разогрева и раскатки. Резина — как тесто для печенья. Пока вы его не испекли, можно несколько раз перемешивать, оно упругое и мягкое.
Клееную резиновую обувь — традиционные азиатские галоши, высокие галоши для сельскохозяйственных работ — изготавливают вручную на механизированных ленточных конвейерах. Работники последовательно накладывают на металлическую колодку текстильные и резиновые детали, которые уже обработаны клеем и мазью на основе натурального каучука.
Собранную заготовку покрывают лаком, помещают на рамки специальных вагонов и отправляют в автоклав, где под воздействием давления сжатого воздуха и высоких температур происходит процесс вулканизации с превращением резиновой смеси в эластичную резину.
При сборке одной галоши выполняется более 30 ручных операций. Это очень трудоемкий процесс.
После вулканизации резиновым сапогам нужно время, чтобы остыть. Далее работники цеха срежут с обуви облой — так называют излишки резины, которые остаются после сборки и обработки. Конечный этап — маркировка обуви, упаковка и отправка покупателю.
Методом формования изготавливают резиновые формовые сапоги общего и специального назначения, формовые морозостойкие галоши на валенки, полимерный низ для комбинированной обуви.
Такую обувь изготавливают методом формования в пресс-форме электрического вулканизационного пресса. При этом происходит воздействие высоких температур и давление сжатого воздуха, подаваемого внутрь резиновой эластичной камеры (дорна).
При сборке сапог на сердечник с мягким дорном вручную надевают трикотажный чулок из хлопчатобумажных нитей, являющийся внутренней подкладкой, затем накладывают резиновые детали. В случае изготовления специальной обуви устанавливают дополнительные детали — ударозащитные подноски и антипрокольные стельки. Сердечник с собранной заготовкой отправляют в электрический пресс для прохождения процесса вулканизации.
— Вулканизация длится от 6 до 16 минут в зависимости от модели обуви, состава резины. Температура — 185—200 градусов, — поясняет директор ТЗРО Елена Шайдюк.
На заводе отмечают, что формовая обувь имеет хорошие эксплуатационные характеристики: прочность, износостойкость, противоскользящие свойства, самоочищаемость протектора подошвы, непромокаемость. За счет специальной рецептуры резиновых смесей обувь получает защитные свойства от воздействия агрессивных химических сред, неблагоприятных воздействий нефтепродуктов, жиров и масел, а также температурных факторов (повышенные и отрицательные температуры).
Елена Шайдюк отмечает, что заводу сейчас не хватает рабочих рук, мало молодежи. Основной контингент предприятия — взрослые люди, которые работают здесь не один десяток лет. Они — носители уникальных знаний. В данный момент заводу резиновой обуви требуются прессовщики, которые занимаются формированием резиновой обуви, обрезчики, маркировщики, упаковщики.
Год назад томский завод купил специальное оборудование для переработки бракованной резины в крошку мелкой фракции. Вторсырье используется для изготовления новой продукции: такую крошку добавляют в каблуки, резиновые шлаги.
Переработка брака и отходов позволяет оптимизировать общий производственный процесс и сделать его безотходным, говорят в компании.
Обувь, которую льют
Теперь поговорим про литьевую обувь. Ее делают из полиуретана (ПУ), поливинилхлорида (ПВХ), термоэластопласта (ТЭП), этиленвинилацетата (ЭВА).
В начале нашего материала мы упоминали, что завод резиновой обуви недавно приобрел две итальянские литьевые установки. Это высокотехнологичное оборудование представляет собой габаритные агрегаты карусельного типа; по периметру установлены пресс-формы, есть устройства для впрыска расплавленного полиуретана, а также роботы-манипуляторы для обработки готовой обуви.
Оборудование предназначено для выпуска цельнолитой и комбинированной полиуретановой обуви с двухслойной подошвой: с промежуточным слоем из вспененного полиуретана и ходовым слоем подошвы из ТЭП или резины. Для голенища комбинированной полиуретановой обуви применяют многослойные материалы на основе ламинированного тканью неопрена.
Для создания полиуретановой обуви в швейном цехе делают специальные чулки. Из текстильного материала выкраивают заготовки, а затем сшивают их.
Чулок-подкладку надевают на металлический сердечник пресс-формы, который создает пространство для ноги внутри обуви. Затем устанавливаются композитный подносок и антипрокольная стелька (если предполагается изготовление специализированной обуви). В последнюю очередь надевают деталь из вулканизованной резины для ходового слоя подошвы.
Пресс-форма машины — это, можно сказать, большие чаши с формой сапога. Под каждую модель обуви и под каждый размер существует своя пресс-форма.
Включают автоматический цикл вращения карусельной установки. Пресс-форма плотно закрывается, после чего происходит последовательное автоматическое впрыскивание горячей смеси изоцианата и полиола. В результате химической реакции образуется полиуретан, принимающий форму изделия.
Примерное время изготовления одного сапога — минута, отмечают на заводе резиновой обуви. Почти весь процесс происходит внутри аппарата. Литьевые агрегаты управляются с помощью компьютерной панели. Для каждой пресс-формы задаются свои настройки — разный размер подразумевает подачу разного объема материала, под разным давлением.
— Машина, с одной стороны, простая: все загрузил и получил изделие. Но чтобы она так работала, нужны тонкие настройки, — говорит директор ТЗРО.
Конечная обработка обуви производится вручную. Когда сапог выходит из формы, у него виден облой (излишки материала). После остывания обуви эти излишки срежут работники производства. Далее — маркировка, упаковка и отправка.
Выпускаемые модели полиуретановой обуви предназначаются как для повседневной носки, так и для выполнения профессиональных работ, говорят на заводе. Для предотвращения возможного механического повреждения ног в конструкции обуви предусмотрены защитные элементы: композитный противоударный подносок и неметаллическая противопрокольная стелька.
Литьевая обувь из ПВХ тоже изготавливается на литьевых агрегатах карусельного типа.
На металлический сердечник пресс-формы надевают трикотажный чулок, являющийся внутренней подкладкой обуви. Пресс-форма закрывается, туда впрыскивается расплавленная композиция поливинилхлорида. По завершении выполнения каруселью полного круга пресс-форма автоматически открывается для снятия с сердечника готового изделия.
Литьевая обувь из ПВХ рекомендована для активного отдыха, купания в бассейнах и открытых водоемах, для повседневной носки при дождливой погоде в весенне-осенний период.
Производство обуви из этиленвинилацетата (ЭВА) происходит похожим образом.
Процесс начинается с помещения гранул ЭВА в сушильную камеру: там они предварительно нагреваются до температуры в 30 градусов. Обувь изготавливают в пресс-формах: расплавленный материал впрыскивают в полость, она начинает обретать форму. Далее обувь достают и еще горячей одевают на колодку, чтобы закрепить нужную форму изделия. Обувь из ЭВА отличается повышенной легкостью.
Нельзя не отметить, что литьевой метод создания обуви требует гораздо меньшего ручного труда. Еще это производство чище, в воздухе нет черной пыли от резины.
Все выше описанные материалы проверяют на соответствие качеству. Контроль происходит три раза в день методом забора уже смешанного материала на выходе из экструдера.
— Почему мы занимаемся всем набором материалов? Все просто — каждый несет в себе что-то лучшее по сравнению с другим, — говорит Елена Шайдюк. — Например, ЭВА — легкая, теплоемкая, но подвержена механическим воздействиям, поэтому такую обувь мало используют как средство индивидуальной защиты ног. ЭВА отлично подходит для производства летних тапочек, к примеру. У резины масса защитных свойств, лучший коэффициент трения с обледенелыми, мокрыми поверхностями. Но производство такой обуви — это довольно трудоемкий и пыльный процесс, нужно много оборудования, много работников. Из полиуретана получается хорошая прочная специализированная обувь и обувь для активного отдыха. Потребители могут выбрать, что им подходит больше.
О планах
До конца года Томский завод резиновой обуви намерен нарастить выпуск обуви из полиуретана. Это возможно благодаря второму литьевому агрегату, у которого недавно завершилась пусконаладка.
Также в планах выпуск специализированной обуви для охоты и рыбалки начиная с 38-го размера.
— Наши наблюдения показывают, что такая обувь интересна и женщинам. Многие сопровождают своих мужей в экстремальных поездках и заинтересованы в хорошей защите ног, — поясняет директор ТЗРО.
По словам Елены Шайдюк, в обозримом будущем предприятие планирует приобрести новое оборудование для производства сапог из материала ЭВА.
***
Вы пользуетесь резиновыми сапогами в повседневной жизни или на даче? Расскажите о своем опыте использования в комментариях ??