Знай город: свет томской лампочки
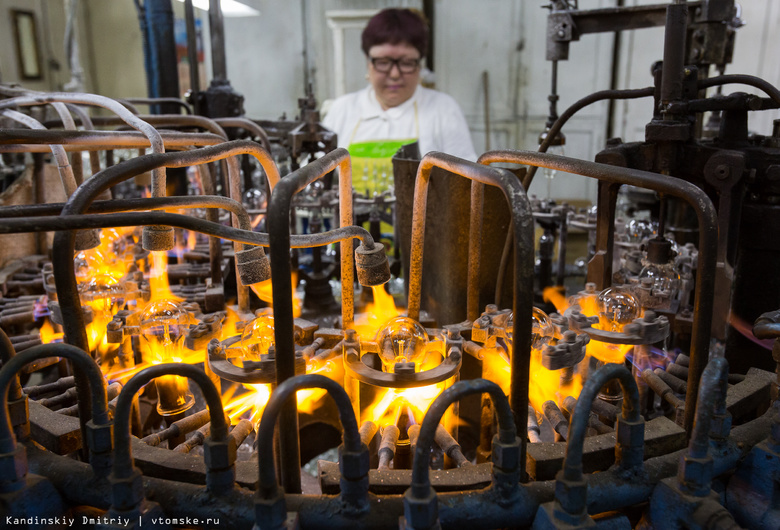
Свет — вещь для нас привычная и обыденная. С одной стороны, это сложное физическое явление — электромагнитное излучение, воспринимаемое глазом. С другой — тот или иной источник освещения. Например, Солнце, Луна или созданная человеком лампа. Данный предмет стал для людей таким же повседневным, как вода или еда. Но, если мы в большинстве случаев знаем о происхождении последних, то много ли мы знаем о производстве лампочек? Дабы раскрыть эту «тайну», мы отправились на томский завод светотехники, чтобы увидеть «рождение» этого источника света своими глазами.
Для начала небольшой экскурс в прошлое. История предприятия началась в конце 1941 года, когда в Томск были эвакуированы несколько десятков работников Московского электролампового и Запрудненского стекольного заводов. Вновь создаваемому предприятию был выделен недостроенный корпус медицинского института. Первая продукция была выпущена 7 ноября 1941 года. Днем рождения завода считается 15 декабря того же года, когда была изготовлена первая тысяча авиационных ламп.
Более чем за 70 лет работы на заводе произошло множество изменений, далеко не всегда положительных. Однако на производстве это не сказалось, предприятие продолжает функционировать и выпускать ежемесячно в среднем шесть миллионов лампочек разных типов и видов.
Как пояснил нам руководитель томского завода светотехники Владислав Голубев, производство лампочки — сложный технологический процесс, состоящий из множества этапов. Их можно разделить на три основных: энергетический этап, относящийся к вспомогательному производству; заготовительный, где идет создание полуфабрикатов; и сборочный этап.
70 % используемых в создании лампочек материалов завод готовит сам и только остальные 30 % — докупаются. Колбы ламп наполняются инертными газами, за счет чего увеличивается их срок службы. На территории предприятия осуществляются процессы по получению водорода, кислорода, азота, а также смешивание газов.
Как пояснила директор по производству и качеству завода светотехники Людмила Малофеева, кислород и азот в жидком виде привозит специальная машина и сливает их в нужные емкости, после чего начинается процесс регазификации. Процесс получения водорода происходит внутри специальной установки.
«Лампы наполняются аргоном. Но чистым веществом наполнять нельзя, так как лампы будут взрываться. Поэтому аргон смешивают с азотом, которого добавляют от 12 % до 16 %. Данная смесь накапливается в емкости. Далее идет очистка газа, а после он подается по трубам на завод для наполнения ламп», — рассказала Людмила Малофеева.
Также предприятие изготавливает свои токовые вводы на отдельном производственном участке. Вначале идет перемотка и очистка проволоки. Несколько машин осуществляют спаивание трех проволок из никелированной стали, меди или ферроникеля. Готовые электроды отправляют на сборочное производство.
Непосредственное производство лампочек — процесс довольно жаркий. Речь, конечно же, о температуре в помещениях. В частности, это обусловлено тем, что на территории предприятия установлена огромная стекловаренная печь, внутри которой больше тысячи градусов. Она производит колбы ламп и другие полуфабрикаты круглосуточно; всего за сутки — порядка 13 тонн стекла. Корпуса ламп из печи выходят раскаленными до 200 градусов. Они движутся по длинному конвейеру, благодаря чему успевают немного остывать, чтобы оператор на выходе смог работать с полуфабрикатом в перчатках. На данном этапе происходит отбраковка и фасовка колб.
На заводе работают несколько линий, которые выпускают разные лампочки — бытовые на 40, 60, 75, 95, 150, 200 ватт, декоративные лампы, теплоизлучатели. Все производство — автоматизировано и чем-то напоминает карусель, благодаря строению машин и их вращению. На ножку лампы монтируются электроды, тело накала, а также штенгель — деталь в виде трубки, сообщающейся с внутренней полостью колбы, служащая для откачки воздуха и наполнения колбы газом.
«На заварочно-откачном автомате уже смонтированная ножка соединяется с колбой. Далее происходит откачка воздуха из корпуса и наполнение его инертным газом, который поступает по трубам, присоединенным к машине. Вся операция находится под контролем оператора», — рассказала начальник сборочного цеха предприятия Ольга Григорьева.
После наполнения колбы газом запаивается так называемый «носик» лампы и обрезается все лишнее — ненужная часть ножки. Далее намазывается мастика, с помощью которой лампа будет крепиться к цоколю. Его надевают сами сотрудницы. Цоколь на предприятии не изготавливают, а закупают.
«На линии происходит первичное зажигание лампы, чтобы проверить ее рабочее состояние. На автомате подобран специальный режим обжига, так как впервые нельзя подавать сильный ток — можно повредить вольфрамовую нить. Кроме того, обжиг помогает в отбраковке: стенки корпуса лампы, из которых был плохо откачен воздух, покрываются небольшим налетом, зачастую белым. Такие лампы сразу идут в утилизацию», — отметила Ольга Григорьева.
Практически по такой же технологии идет процесс изготовления новых светодиодных ламп, которые были недавно разработаны предприятием совместно со специалистами ТУСУРа. Лампа нового поколения, которую на предприятии прозвали «лампочкой томича», имеет по своим параметрам схожесть с лампой накаливания, особенно в части корпуса. Серийное производство этих ламп пока готовится к запуску — оно запланировано на август.
«Процесс создания новой лампы отличается от основного тем, что операция идет с разрывом, а не потоком. Например, в один день делаются только ножки на конвейере, после чего наступает черед ручного процесса — монтажницы спаивают светодиодные нити. Далее снова начинается автоматический процесс», — пояснила начальник сборочного цеха.
После того, как лампочки собраны и прошли отбраковку, они отправляются на технологическую выдержку на промежуточный склад.
«Каждая лампа должна вылежаться, так как в стекле могут быть микротрещины. Давление внутри лампы — примерно 650 миллиметров ртутного столба, а в окружающей среде — порядка 740. Есть риск, что большее давление передавит лампу, но не сразу, поэтому ей нужно определенное время, чтобы отлежаться — от двух до пяти суток. После продукцию еще раз обжигают для стопроцентной уверенности, что нет брака», — подчеркнула Ольга Григорьева.
Как и на любом производстве, на заводе светотехники есть своя лаборатория. В частности, в химической части проводят анализы стекла. В светотехнической — снимаются световые и электрические характеристики продукции. Так, например, здесь лампы испытываются на продолжительность горения при помощи специальных стендов. Эта процедура может длиться до двух тысяч часов. Также в лаборатории стоят несколько фотометрических шаров, которые используют для измерения характеристик ламп. Один из шаров достигает трех метров в диаметре. Прибор такого размера используют для измерения параметров больших светильников.
На этом производство не заканчивается. На территории предприятия есть картонажный цех, в котором делают гофроманжету.
«На двух гофроагрегатах изготавливается двухслойный картон путем склеивания двух листов бумаги. Один рулон такой бумаги весит 570 килограммов. Далее идет процесс гофрирования и разрезания картона на материал нужного размера. Готовую промежуточную продукцию упаковывают и отправляют на производство», — рассказала Ольга Григорьева.
После того, как лампочка отлежалась на промежуточном складе, она отправляется на конечную фасовку и на прилавки магазинов. Также продукцию можно найти в специальном магазине, расположенном в здании завода.
Другие материалы рубрики читайте по ссылке.